
Terminating MI cable (see illustrated procedure below)
General procedures for terminating are provided below. Be advised that MICC cannot be responsible for the effectiveness of terminations because we have no control over the fabrication of these items.
The environment should be clean and dry. Tools should be in good working order and used for the purpose that they are designed. Terminating materials must be of MICC type and be compatible with the cable.
Cable cutting
Cable cutting is carried out before terminating. Always allow for an amount of waste (usually 0.1 m) during fabrication or repair. Ensure the correct cable is selected and load it onto a swift or payoff – measure the length through a cable measurement wheel or by carefully using a rule.
The cable should be cut squarely to the length required allowing for the appropriate length of conductor tails. The cable may be cut with heavy-duty side cutters, bolt cutters, or even an abrasive saw. The cable should be temporarily sealed by heating the end of the cable with a gas blowtorch and applying hot melt glue to effect a moisture seal.
When a gland shroud is to be used, cut the cable end square, and then offer up the shroud to the cable end in reverse to determine the amount to be cut off, to ensure a tight fit over the outer covering.
Then mark and strip the copper sheath as shown or described below.
This should be repeated for each new cable length required.
Using a Fork Ended Stripping Rod
Fork Ended Stripping Rods for all cable sizes can easily be made on-site from a suitable piece of rod, the end being slotted with a hacksaw; a typical tool is illustrated. Start the ‘rip’ with side cutters, as in the previously described method. Pick up the tag in the slot of the rod and twist it around the cable. Retain a 45° angle to the line of the cable allowing the swarf to spiral along the stripping rod. Break into the groove and finish with side cutters as with the method previously described. After the removal of any remaining insulant from the conductors, the cable is now ready for sealing.
Using MICC Ringer
Rotate the MICC Ringer around the cable for one complete turn, or more if the first cut appears shallow. The correct depth for the groove is half the thickness of the sheath. Just before the ‘rip’ enters the groove bring the side cutters to right angles with the cable. Break into the groove and turn the side cutters parallel to the cable following the groove around the cable to neatly finish the stripping operation. After the removal of any remaining insulant from the conductors, the cable is now ready for sealing.
Using the MICC Potter ZPM
To order use Ref. ZPM. Recommended for all types of seals when using externally threaded glands, available for all four gland sizes. If the sheath stripping operation has left any roughness around the end of the sheath, this can be removed by lightly running pliers around the cable end, ensuring that no resultant metal particles adhere to the insulant.
Place the gland nut and compression ring on the stripped cable end. Position the pot into the gland body and screw into tool. Finger tightness is not sufficient. The assembly must be lightly nipped up using pliers or a spanner. Slide MICC Potter onto the cable, turning it in a clockwise direction while applying sufficient forward pressure to engage the internal screwthread of the pot onto the cable sheath.
Using Pliers or Grips
This method has the merit of employing a tool normally carried by an electrician and does not require the use of a gland. However, if a gland is being used to terminate the cable, it must be slid onto the cable before screwing on the pot.
If there is any roughness left around the end of the cable sheath from the stripping operation, remove it by lightly running the grips along the end of the sheath, ensuring that no resultant metal particles adhere to the insulant. The pot which has a self-cutting thread should be started by hand, place the parallel entry section of the pot over the end of the cable sheath, push and turn the pot squarely onto the cable using a clockwise rotation. Then grip the knurled base of the pot with the pliers and screw the pot onto the sheath until the sheath is level with the
shoulder inside the pot.
With small diameter cables, it is advisable to grip the cable sheath with pliers just behind the pot, to prevent twisting of the cable. Do not reverse the screwing motion whilst fitting the pot as this can cause slackness of the pot, which can affect sealing performance.
The fitting operation may be assisted by applying a slight smear of oil to the sheath. Taking care to avoid facial contact with the conductor ends examine the pot interior and remove any metal hairs or loose powder that may have resulted from the screwing action.
Cables with 1,2,3,4 and 7 Conductors
Press the RMX compound into the pot from one side only to avoid cavities, keeping the thumb behind the wrapping, to ensure cleanliness. Fill the pot, overfilling slightly. Care should be taken to avoid contamination of the sealing compound. Slide the disc/sleeve assembly up to the pot and press it into the recess in the pot lip with the aid of pliers, applying pressure only to the face of the cap or disc.
The seal is now ready for crimping
Pull the inner conductors straight using pliers. Reposition the next layer of conductors and apply more compound as necessary, before restraightening the conductors by pulling gently with pliers. Taking care to avoid cavities, slightly overfill the pot. Care should be taken to avoid contamination of the sealing compound. Enter the conductors into the disc one at a time, starting with the inner conductors and taking care to achieve correct alignment. When all conductors have been entered, push the disc into the pot recess with the aid of a pair of pliers or another suitable tool.
Crimping the Pot Closure
MICC Crimp Tool Ref. ZDC
Fully unscrew the drive screw using the handle. Slide the conductors through the hole in the crimping plate and the hollow drive screw. Place the pot into the seating in the brass body and tighten the screw until it is fully hand tight which will drive the disc fully into the pot recess and secure it in position.
Fitting the Conductor Insulation
When using discs cut the conductor insulating sleeving to the required length and slide it over the conductors. The seal is now complete. When using PVC headed sleeves the standard length supplied is adequate for most applications.
When longer lengths are required, extension sleeving is available.
Bush Backnut, Body Hexagon, Externally Threaded Glands
Secure the gland body into the equipment by screwing it into a threaded entry or securing it into a plain hole entry using a locknut.
Locate the pot seal in the desired position and tighten the back nut to secure the cable using the compression ring.
Certain types of enclosures have been tested and/or certified as having a specified degree of ‘Ingress Protection’ (IP Rating e.g. IP 54). This rating is determined by assessing the degree of ingress of solids (e.g. dust) and liquids into the enclosure. In some installations, for example, in damp or dusty conditions or potentially explosive atmospheres, it is necessary to specify a minimum IP Rating for enclosures and to ensure that it is maintained when cable entries into the enclosures are affected.
Recommendations as to how this may be achieved should be available from the enclosure/apparatus manufacturer or supplier, who may need to consult the cable gland manufacturers. MICC glands have been tested and it is possible to achieve IP67, i.e. no ingress of dust or water. MICC standard NPT gland threads are machined to at least ‘medium fit’ tolerances, as is the general case with threaded entries in hazardous area apparatus. Based on experience, the following information is offered for general guidance.
Threaded Entries
A rating of IP54 may be achieved with MICC glands tightened in the recommended manner. The entry hole should have at least three threads of medium fit tolerance
(a thread sealant is not normally required). A rating of IP67 may be achieved by using a suitable thread sealant.
Provision of Earth Continuity
MICC brass compression glands that comply with UL requirements have been tested and shown to provide excellent high conductivity earth connections to metallic enclosures. However, where it is envisaged that the earth continuity may be subsequently impaired by corrosion of the enclosure, it is recommended that the enclosure be suitably protected. When enclosures manufactured from insulating materials are used, earth continuity may be obtained using MICC Tag earth tail washers and an appropriate brass cable gland.
Inspection
The seals should be inspected for obvious defects. If there is a minor fault, e.g. incomplete crimping of a brass pot, it may be practical to simply repeat the crimping operation. In the case of major faults, such as significant deformation of a brass pot, it may be necessary to remake the seal.
Testing
Testing of un-sealed cables will result in erroneous and misleading readings. Therefore only cables sealed at both ends should be tested.
After both ends of a cable have been terminated with permanent seals, the cable should be subjected to an insulation test 24 hours later when the IR should be at least 100MΩ. The test voltage should be selected following local regulations for electrical installation. When testing cables connected to equipment the test voltage chosen must take account of the voltage to withstand all the connected equipment.
In some special circumstances e.g. certain types of fire alarm systems, the circuit may comprise a large number of individual cable lengths. For such circuits, it will be necessary to achieve well over 100MΩ IR on each cable length, so that the IR of the complete circuit will meet the commissioning requirements. This will not be a problem providing the cables are correctly sealed immediately after the sheath is stripped back.
Identification
If the IR is satisfactory, the conductors should be identified using a bell set, ohmmeter, or similar instrument and then color-coded per the NEC (or CEC).
Color identification of cores of non-flexible cables and bare conductors for fixed wiring.
When attempting to locate faults on circuits involving multiple cable runs, it is preferable to isolate and test individual cables, to avoid the errors introduced by parallel connections. Faults that occur after cables have been installed and terminated may be short circuits, direct earth faults, or low IR faults. Such faults may be caused by loose connections, trapped leads, damage by other trades, or faulty terminating practice. In the latter case, it is important to differentiate short circuits and direct earth faults from low IR faults before taking remedial action.
Cables should be selected per the requirements of the latest edition of the NEC (NFPA70) or CEC in consideration of local regulations
Installation Design Data
Note:
- Ensure the correct drawings or schedules are available to determine where the cables are to be installed.
- If JBs and other ancillaries are also fixed ensure their fixing arrangements are installed before cable installation to avoid interference
- Compare cable tag information with information in 1) and confirm length and type – check this label carefully!
- Inspect the cable and accessories for damage
- Check the IR of each cable using a 500V IR tester (Megger). The minimum acceptable IR shall be 100 MΩ
- WARNING – cables failing MUST not be installed and either returned to MICC Ltd. for repair or repaired locally – please contact MICC Ltd. for advice
- Ensure that all metal joining processes on the installation has been completed.
- Check before installation that actual install lengths and actual available lengths are comparable
- Ensure that the installation surface is free from burrs, nicks, and sharp edges. These could cause damage to cables during installation and are also a hazard to the installers
- Check that any surface treatments (paint, coatings, etc) have been considered and have been completed.
- The radii of any curves should be left as large as possible to allow for any subsequent adjustments.
- After the cable has been installed it may be necessary to adjust for excess or shortage of cable length by redistribution on the installed surface. Severe mismatch should have been checked before installation but, if necessary, the project engineer responsible should be informed so an appropriate decision can be taken.
In all cases, reference must be made to NEC (NFPA70) or CEC (specifically refer to Article 332 of the NEC code NFPA 70 for regulations on installation) then local regulations for the state (or province) must be considered for:-
- Cable ampacity
- Volt drop calculations
- Installation methods being considered
- Derating of ampacity
- Earthing/grounding – the size of the protective conductor
- Any other correction factors for the installation
For particular applications please refer to NFPA70 for guidance searching ‘Type MI’, ‘mineral-insulated’ or ‘mineral’.
Surface Preparation
It is good practice to ensure that the surface is clean and free from rough areas, sharp edges, or burrs that could cause damage to the cables during installations.
All welding or mechanical engineering site work should be completed before cable installation begins.
Good practice – test the Insulation Resistance again (IR)
Before starting the installation the cable to be installed should be checked for IR using a 500 volts IR tester (Megger) connected across the conductor(s) and the metallic sheath and conductor to conductor. It should not be less than 100 MΩ. However, site conditions may reduce this and a value of 20 MΩ is considered to be acceptable even in dry conditions. Wet conditions may reduce this even further but in any case, a value of <5 MΩ should be considered evidence of a problem to be investigated.
Mounting materials and substrate
MICC should be installed and supported on suitable materials – seek guidance from MICC if necessary. Installation should be made on the substrate which is designed to withstand the effects of fire – typical substrates are concrete or reinforced concrete used for the construction of high occupancy buildings or those buildings which need to provide a fire withstand capability such as gas filling stations.
Cable fixings
When installing any life-critical circuit, it is essential that the cable fixings will be able to support the cable before, during, and after a fire and will not contribute to the ignition or spread of the fire. If the fixings are inadequate, the cable can sag or come away from the wall or tray. Unfortunately, this will render today’s inferior fire-resistant cables useless in a fire.
Only use support materials that complement the benefits of MICC cables.
Cable supports must have 2-hour fire-rated capability – only the recommended approved support components will offer the 2-hour fire rated approval.
The cable should be installed per NEC article 300 (specifically 300.4) and Article 392
Temperature
Bare sheathed cables can be installed at temperatures down to -30 deg F (-35 °C C).
When preparing the cable for installation to the working area, and in coil format, carefully unroll the coil. DO NOT pull out into a spiral. Avoid twists or kinks. Wherever possible avoid installing the cable over rough surfaces and take precautions over sharp edges to prevent damage to the cable.
When the cable runs have been completed ensure that the slackness due to excess length is evenly distributed along the whole length of the cable run.
Insulation resistance
IR (IR) should be checked before installation. Using a typical 500Vdc Megger follows conventional IR checks between conductors and conductor to sheath – IR readings should be higher than 100MΩ. If the IR is below 20 MΩ the IR can be recovered by warming the cable using a heat source starting 6 inches from the end of the cable, seal, and wait 12 hours to see the IR recover.
Vibration
MICC Cable is sufficiently pliable to carry the supply to motors and other equipment where slight differential vibration may have to be contended with. Such vibration can be absorbed by introducing a loop in the cable immediately before it enters the enclosure. In cases of severe differential vibration, the cable should be terminated into a junction box adjacent to the vibrating equipment, and the final connection made via a flexible conduit and/or cable.
Office Address
26695 Eckel Road, Suite B, Perrysburg,
Ohio 43551
USA
[email protected]
Phone: 567-331-0101
Cell: (419) 575-7220
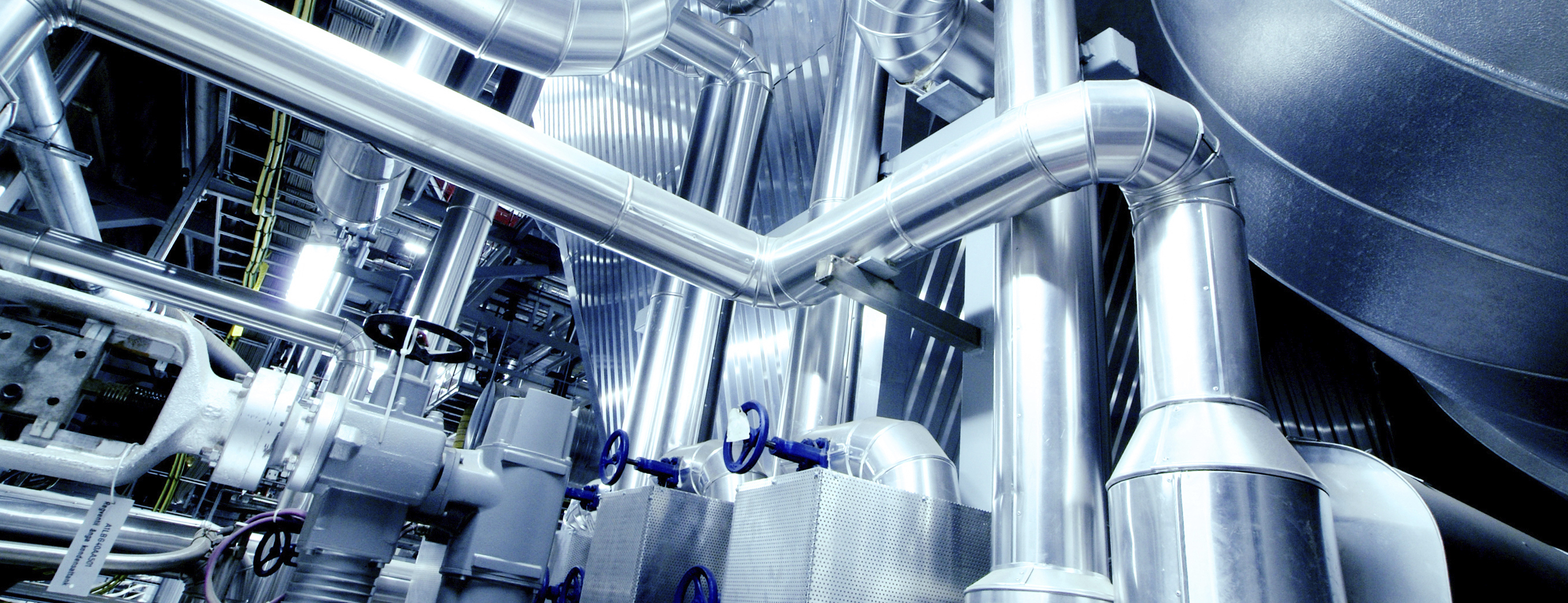